Turning and machining
Modern production plant delivering high performance
Manufacture is carried out using single and multiple-spindle lathes with digital and conventional controls.
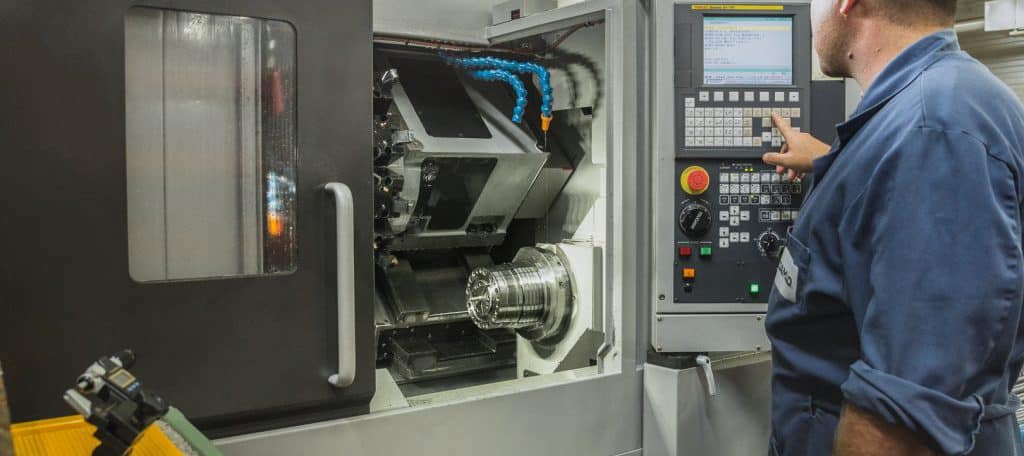
Multi-spindle turning
- 7 lathes, capacity: diameters of 5-48mm Ø 5 à 48 mm
Conventional single-spindle turning with sliding headstock
- 9 lathes, capacity: diameters of 3-20mm
Digitally controlled turning with fixed headstock
- 17 lathes, capacity: diameters of 5-80mm, including:
- 4 Okuma 7-axis lathes, bar diameter: 65mm
- 1 MORI SEIKI NLX2500 lathe, bar diameter: 80mm
- 1 BIGLIA B438Y2 lathe, diameter: 42mm
- 1 BIGLIA B445 lathe
- o 1 MIYANO ANX42 lathe, diameter: 42mm + long part production
- Can machine 200mm-diameter slugs
Digitally controlled turning with sliding headstock
- 15 lathes, capacity: diameters of 3-38mm, including:
- 3 Citizen E32 lathes
- 4 Citizen L20 lathes
- 1 Star ST38 lathes
- 2 Star SB20 RJ lathes
- 1 Star SR20 lathes
- Maximum machining length: 3 000 mm
Machining centres
- 6 machining centres, including:
- 2 KIA VX380T0 (palettized)
- 1 KIA VX500
- 1 KIA F500Y with 1000mm table
- 2 KIRA with 1500mm tables

Finishing turned parts
- 4 transfer machines, 6-8 work stations
- Conventional finishing shop
(lathes, drilling machines, milling machine, tapping machines)
High-precision grinding for machined parts
- 7 Centreless machines for through-feed grinding
- 4 Centreless machines for in-feed grinding
- 4 STUDER cylindrical grinding machines (including one for thicknesses of up to 1600mm)
Assembly of turned parts
- 2 Turning presses
Boring
- IMSA two-spindle, double-head deep hole drilling machine (max. length: 1500mm)
Grinding and finishing
We have transfer machines, machining centres and automated modules for finishing, as well as cylindrical and centreless grinding machines.